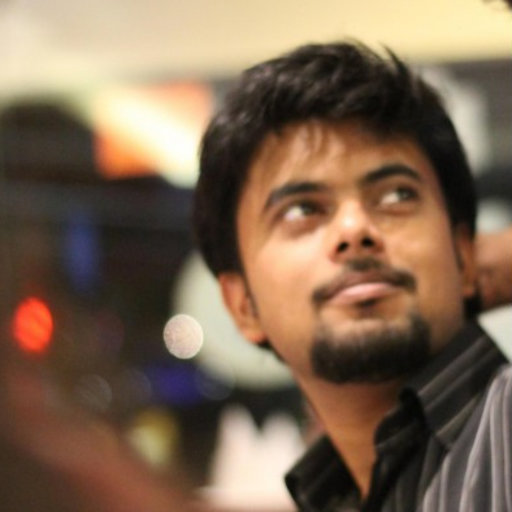
Given that ExpEYES17 has more than a hundred tiny components, assembly by hand takes a few hours each. This is impractical due to cost considerations, as well as the high probability of human error.
These formidable machines automatically populate PCBs, and leave little room for error. The automatic assembly is a multi-step process
Gather component reels/tubes/trays, and load them into the many feeders of the pick and place machine.
We use a large number of 0805 sized components, and you can see the rolls in this picture. The sharp vacuum nozzles of the machine can easily place these parts with a high level of accuracy.
You can also see a tray of TQFP package microcontrollers
Solder paste is applied on the PCB via a stencil. Each point that needs to be soldered is applied with a thin layer of solder paste which is mix of powdered solder(Lead and Tin alloy), and flux(chemical which aids in cleaning oxide layers).
The machine is an incredible piece of engineering. It picks up a dozen tiny parts within a second, and we had to make a slow motion video to see it in action. Each part is picked up by one of twelve vacuum nozzles arranged in a circular pattern. The nozzle array rotates to let the next nozzle load a component.
Once each of the nozzles are holding a component , the whole arm moves onto the PCB, and places the components where they need to be. Rinse and repeat!
Also not that there is already a layer of solder paste between each component’s pins and the PCB’s pads.
Slow motion video of a Pick and Place PCB assembly machine loading components into a circular array of vacuum nozzles, and placing them on the ExpEYES17 circuit board which we aided in development and also manufacture.
Two arms are faster than one!
At this point the components are all delicately placed on the solder paste, and they can be moved around if necessary.
Once this board goes through the reflow process, it’s ready to be shipped/packed, and alterations are akin to repair. So a good look is advisable.
The reflow process involves heating the entire board to a certain controlled temperature at which all the solder paste melts, and joins each component’s pins to the corresponding pads. The components are not damaged because they are rated to survive these high temperatures ( 270 degrees typically)
If the solder paste was applied accurately via the stencil, and the pick and place machine did not make any offset errors, the entire board is ready to use after the reflow process. Occassionally the machine may make mistakes with a component or two, and this is rectified after visual inspection.
The reflow oven can either be of a fixed type, or a conveyor type. The reflow process involves a series of different temperatures set in a certain order known as the temperature profile.
While the fixed type needs to adjust its temperature accordingly over the duration of the enture process, the conveyor type simply needs to maintain different temperatures at different zones as the PCB slowly moves through it and gets reflowed.
If your PCBs are heading out to rough environments, it may help to spray coat them with acrylic to protect it from the elements.